What Is It:
Advanced Product Quality Planning (APQP) is a structured approach to product development that ensures quality and efficiency from concept through production.
An integrated APQP methodology brings together all stages of product planning, aligning cross-functional teams and ensuring that quality standards are met throughout the process.
This approach is widely used in industries like automotive and manufacturing, where consistent quality and reliability are essential.
Why It Matters:
Implementing an integrated APQP methodology is critical for companies aiming to improve product quality, reduce risks, and ensure smooth product launches.
- APQP reduces product development time by up to 30% by streamlining processes (AIAG).
- Companies using APQP report a 25% improvement in product quality and reliability (Deloitte).
- APQP implementation can reduce production defects by 40%, leading to higher customer satisfaction (McKinsey).
By integrating APQP into product development, organizations can improve quality, minimize rework, and deliver reliable products that meet customer expectations.

How It Works:
The APQP methodology is structured into multiple phases, each ensuring quality and efficiency throughout the product development lifecycle.
- Plan and Define Program: Identify customer needs, set objectives, and outline key project requirements for a strong foundation.
- Product Design and Development Verification: Create and verify product designs that meet both quality standards and customer expectations.
- Process Design and Development Verification: Develop and validate production processes that align with the product design and quality goals.
- Product and Process Validation: Conduct tests and validations on both the product and processes to confirm they meet performance and quality specifications.
- Feedback, Assessment, and Corrective Actions: Collect feedback, evaluate outcomes, and apply corrective actions to address any issues and improve processes.
- Establish Control Plans: Develop detailed control plans to maintain product quality during full-scale production.
- Risk Assessment and Mitigation: Identify risks within product and process designs and create strategies to minimize potential impacts.
- Supplier Quality Management: Engage suppliers in the APQP process to ensure they meet quality standards and support the project goals.
- PPAP (Production Part Approval Process): Approve production parts based on quality standards before full-scale manufacturing begins.
- Documentation and Record Keeping: Maintain comprehensive documentation at each stage for traceability and compliance.
- Continuous Improvement: Regularly assess and refine APQP processes to adapt to evolving standards and drive ongoing quality enhancements.
By following these globally recognized steps, organizations can ensure that quality is embedded into every phase of product development, leading to reliable products and satisfied customers.
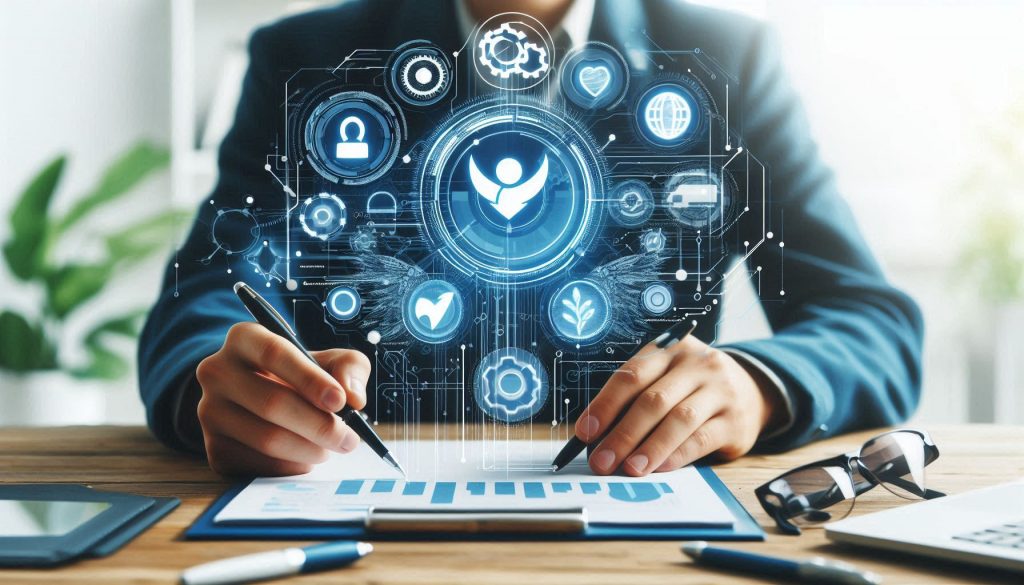
The Value Proposition:
- Enhances product quality and reliability by embedding quality controls into each development phase.
- Reduces time-to-market through streamlined, standardized processes.
- Minimizes defects and rework, leading to cost savings and improved customer satisfaction.
The Global Standards:
- AIAG APQP Standards (USA): The Automotive Industry Action Group’s APQP standards provide a comprehensive framework for product quality planning.
- ISO/TS 16949 Quality Management (Switzerland): Offers international guidelines for quality management systems in automotive production.
- PPAP (Production Part Approval Process) (USA): Complements APQP by ensuring parts meet quality and design specifications before production.
The Bottom Line:
An integrated APQP methodology ensures that quality is maintained throughout product development, resulting in reliable products and satisfied customers.
The Question:
Is your organization using an integrated APQP methodology to ensure quality and efficiency in product development?
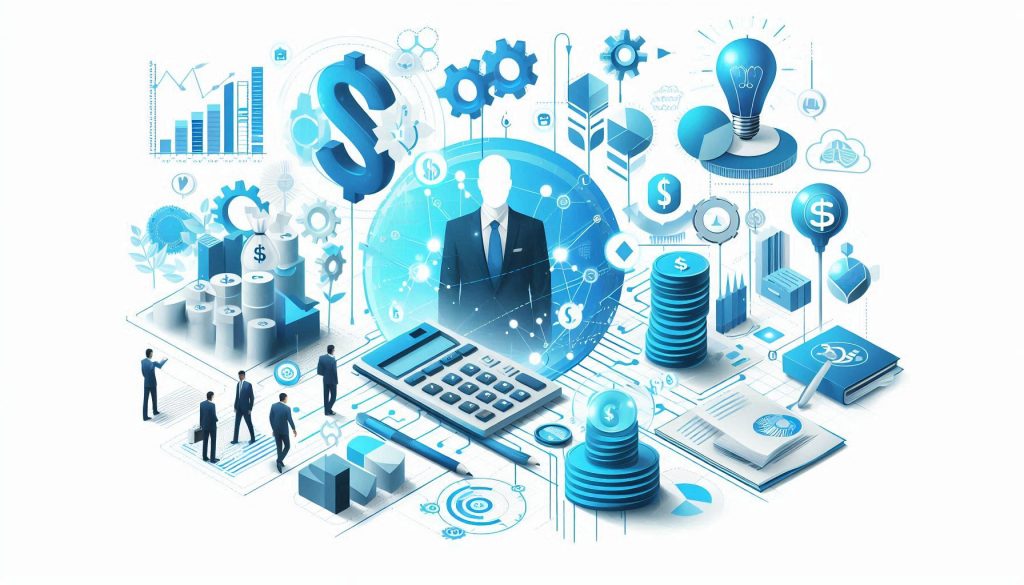
How Arience Can Help You:
- Consulting: We help organizations implement integrated APQP frameworks tailored to their industry requirements.
- Mentoring: Our team mentors project and quality teams to ensure effective APQP adoption and execution.
- Coaching: We provide coaching for individuals, helping them develop skills in APQP and quality management practices.
Why Choose Us:
- Expertise in APQP Implementation: Extensive experience guiding organizations through APQP adoption across various industries.
- Customized Quality Solutions: Tailored APQP frameworks that align with your organization’s quality and production goals.
- Focus on Measurable Quality Improvements: Committed to delivering improvements in product reliability, defect reduction, and customer satisfaction.
The Next Step:
Ready to implement an integrated APQP methodology for enhanced product quality? Contact Arience today for expert guidance and customized solutions.
Copyrights, Acknowledgement & References:
- Center for Creative Leadership® (USA): Provider of tools and standards for effective 360° feedback programs.
- ISO® (Switzerland): Publisher of ISO 30414 for human capital reporting standards, including feedback metrics.
- SHRM® (USA): Offers guidelines for integrating feedback into employee development strategies.